Table Of Content
Student teams will design, fabricate, and demonstrate the flight capabilities of an unmanned, electric powered, radio-controlled aircraft which can best meet the specified mission profile. Began with high expectations after 2022, this year required a highly efficient plane that could fly the heaviest payload for the most laps, while also holding the largest weight via the wingtips during ground mission. While this year saw all on-campus activities return to normal, manufacturing had to be rebuilt from the ground up in order to facilitate the high strength carbon sandwich construction necessary for the aircraft’s design. While competition was not controversy-free, the team ultimately came through, scoring a record 5th place out of 99 teams. This year’s flight objective was to design, build, and test a remotely operated radio control airplane for Urban Air Mobility.
Utah State University Students Excel at National Aviation Maintenance Competition
To minimize the drag in Mission 3, a twin-boom, twin-motor monoplane configuration with an H-tail empennage was chosen. The twin-boom configuration was chosen to separate the two rows of attack stores to reduce drag, and to distribute the load on the wing. The twin motor configuration also allows differential thrust for yaw control, eliminating the need for rudders. The wing is designed to fold along the chord to reduce the span from 6.07 ft to 2.75 ft in the folded configuration. A conventional monoplane configuration with a twin-tractor propulsion system was selected. The shape of the fuselage is designed to carry 8aluminum bars in a single file line to minimize profile drag.
The Competition
Teams then competed in various military themed missions and as usual, the total score was a product of the flight scores and written report scores. The UW DBF team participated with the “Puget Sound Barrier” and placed within the top 1/3 of competitors. The UW design, built, and flew a “Joint Strike Fighter” aircraft with internal payload capability. The competition consisted of missions involving short take-off and landing, stealth missions, and strike missions. The “DawgAir 313” was designed to meet these design requirements using a unique morphing wing technology.
Search Utah State University:
As most people know, at Flite Test we make airplane build kits that make it incredibly easy to build and fly your own RC aircraft. Flying RC can be very technical and sometimes it’s nice to eliminate guess work by having an airplane that is just ready to go. The disadvantage to these ready to fly aircraft is that they can be difficult to repair after a major crash.
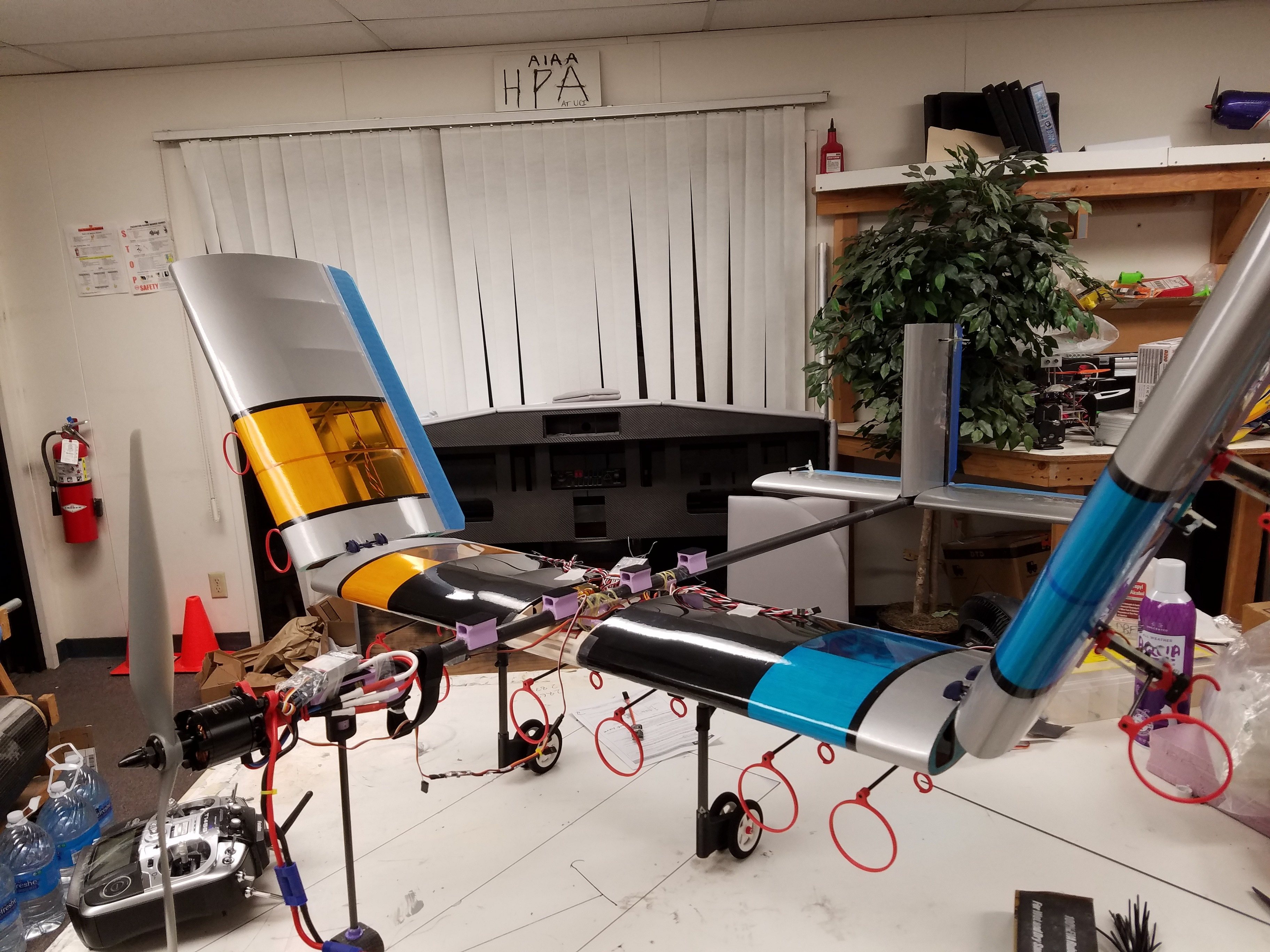
Hollow-molded composite construction techniques for the aerodynamic surfaces andfuselage maximized the structural efficiency of the aircraft and minimized aircraft weight. After a year’s hiatus, the UW DBF team participated in their second AIAA Design Build Fly Competition. The aircraft was designed to carry an range of volume- and/or weight-intensive payloads. Despite this only being the second year of entry, the team was one of only seven teams to complete both flight missions. Design for the year focused on the creation of a UAV capable of deploying, towing, and retrieving an internally-stowed mock sensor, and capable of ferrying a high number of these sensors.
A tail dragger landing gear configuration was chosen to minimize drag while simplifying banner loading. Due to the takeoff distance constraints of Missions 1 and 3 and the emphasis on large amount of payload the wing was designed to be high lift while not sacrificing too much performance during cruise. To minimize the wingspan, a dual counter-rotating motor, biplane configuration with a cruciform empennage was chosen. As the aircraft has an unusually short span, the wings are incapable of producing significant roll stability. The aircraft uses two counter-rotating motors resulting in no net torque on the aircraft from the propulsion system.
The Manufacturing Aircraft (Mark IV) was designed to fit aroundthe Production Aircraft, resulting in a Manufacturing Aircraft comprised of two sub-assemblies with hollowwings and tails. Instead,stability control is provided by ailererons augmented by a rudder and elevator for both aircraft. To encourage innovation and maintain a fresh design challenge for each new year’s participants, the design requirements and performance objective will be updated for each new contest year. The changes will provide new design requirements and opportunities, while allowing for application of technology developed by the teams from prior years.
To minimize aircraft weight and size, the rear wingdoubles as a horizontal stabilizer. The aircraft has two vertical stabilizers to achieve a simple foldingmechanism while maintaining symmetry. All aerodynamic surfaces fold along the fuselage to transitionthe aircraft from the flight condition to the stowed condition. Together, a belly skid and tail guard ensure safe landings while minimizing thesize and weight of the aircraft.
Students working with the team will develop skills with products that will carry over to their professional careers. DBF gives students the opportunity to explore a variety of disciplines within aeronautics and apply what they learn in classes in a setting similar to that of industry. The packages were also equipped with shock sensors that nullifies the score of a deployed package if tripped. Unfazed by the challenges and adversity, the team managed to successfully deploy 6 packages, the third most of 97 teams, and scored the highest finish of 9th, marking the return to competitiveness. During the fall quarter, 2021, we finished our preliminary design of our aircraft including the fuselage, wings, tails, and landing gears.
Over the course of the year, we design, analyze, prototype, and fly numerous aircraft for a given competition. The aircraft is required to carry vaccine vial packages as its payload and must fly the standard mission profile for each lap. However, the aircraft is required to land anywhere on the runway and taxi to the designated vaccine vial package drop area. The aircraft must repeat the procedure until all vaccine vial packages have been delivered to the designated destination (minimum 1 vaccine vial package is required to be delivered) within a 10 minute flight window. The scoring function for the competition indicates that aircraft top speed, which is impacted by aerodynamic design and correlates with the propulsion system mass fraction, are the primary design drivers.
Teams were assigned payload manifests at random and scoring was based on performance during these runs. The UW successfully design, built, and flew “The Growler”, a unique bi-plane configuration with high speed and payload capacity. The aircraft must complete three laps within a 5 minute flight window for this mission. In order to minimize the number of sub-assemblies of the Production Aircraft (Tony), which adversely affects theRAC, a single sub-assembly design was chosen and built.
Though challenged with remote-design work, reduced manufacturing access, and a remote, video-based competition flyoff, the team responded with the largest aircraft, and first tandem wing that DBF at UW has produced. A pre-competition crash precluded the ability to perform the third and final flight mission, dramatically influencing the team’s final score. Students are required to keep up with changing technologies and mission requirements as the aerospace industry advances.
Onward and upward with the USC AeroDesign Team - USC Viterbi School of Engineering - USC Viterbi School of Engineering
Onward and upward with the USC AeroDesign Team - USC Viterbi School of Engineering.
Posted: Fri, 02 Jun 2023 07:00:00 GMT [source]
This year’s competition involved designing an aircraft to accommodate a random assortment of payloads. While the UW was able to construct and submit a final report for “Da Dawgsled”, technical issues prevented any competition flights of the aircraft, dramatically impacting the final score. The airplane had to fit in a commercially available suitcase meeting airline carry-on requirements.
Student teams design, fabricate and demonstrate the flight capabilities of an unmanned, electric powered, radio-controlled aircraft to meet the specified mission profile. The goal is to create a balanced design with good flight handling qualities, practical and affordable manufacturing requirements and high vehicle performance. Each year students of the University of Washington take part in the AIAA Design, Build, Fly (DBF) competition. Teams from over one-hundred institutions must design, fabricate, and demonstrate the flight capabilities of an unmanned, electric, radio-controlled aircraft that best meets specified mission profiles.
The airplane must be able to conduct a delivery flight, a medical transport flight, and an urban taxi flight. Teams also conducted a ground mission demonstrating how quickly they can change their aircraft configuration from delivery to medical transport to urban air taxi. This year's flight objective was to design, build, and test a remotely operated radio control airplane for Urban Air Mobility. A traditional twin-tractor monoplane aircraft configuration with a conventional tail and custom dual-purposelanding gear was selected. A two-skid landing gear configuration withminimally protruding wheels was developed to address the requirement that the landing gear be identicalfor flight missions and the rough field Taxi Mission. The skids provide optimal maneuverability over thecorrugated roofing panel in the Taxi Mission, and the protruding wheels maintain a low-friction interface for takeoff roll.
No comments:
Post a Comment